Resources
How to set the parameter standard for injection molding process
Release time:2023-10-19
How to set the parameter standard for injection molding process
1. Injection speed:
① Slower injection speed, the plastic in the mold cavity, there will be more heat loss, flow viscosity increases, the use of pressure loss increases;
② Higher injection speed tends to get higher precision, less deformation of molded products, only through the meat thickness of small, intense changes, corners and other areas, prone to poor appearance, and prone to poor exhaust, batch front, and holding pressure switching incorrectly and other issues.
2. Switching of holding pressure:
① Too early switching, the finished product size is easy to be insufficient, or even short shot, and surface depression, and vice versa, the formation of excessive compression, small is too large size, flying edge, whitening, deformation, large is the use of the mold is damaged;
② The switching of holding pressure is usually controlled by injection stroke (position) and time.
3. Holding pressure size setting:
① Holding pressure is too high, overfilling will occur, which makes the plastic already in the mold cavity backflow;
② Correct and appropriate holding pressure setting, should make the screw through the holding pressure switching point can continue to push to the target point of the lower pressure as a principle;
③ In the holding phase, the pressure inside the mold cavity gradually decreases due to the cooling of the plastic, so the holding pressure should be appropriately followed by the adjustment of the drop, otherwise it is easy to form a high stress residual.
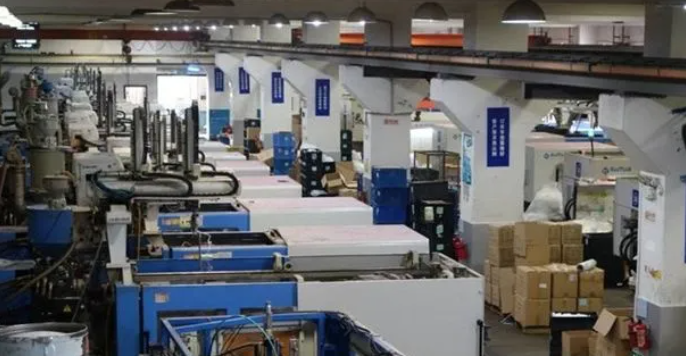
4. Setting of holding time:
① The holding time should be maintained until the sprue has condensed; too long a time is meaningless, but too short a time will tend to reverse the flow, making the near-gate portion of the location susceptible to denting and undersizing;
② The appropriateness of the holding time should usually be judged by the stability of the weight;
③ If the gate is small and the mold temperature is low, the holding time should be set shorter, if the situation is the opposite, then the time setting should be lengthened.
5. Setting of cooling time:
① Plastic cooling in the mold cavity, most of the beginning of the holding pressure switching end of the open mold, the theoretical cooling time = holding pressure time + post-cooling time;
② The theoretical time needed should be the product can be smoothly ejected (no deformation) as a principle, the length of the molding product thickness, material, and mold cooling speed is different;
③ The gate thickness and mold temperature will affect the holding time (the cooling time set by the machine, that is, the after-cooling time). If the gate is big and the mold temperature is high, the holding time should be increased appropriately, and vice versa, the holding time should be reduced appropriately.
、
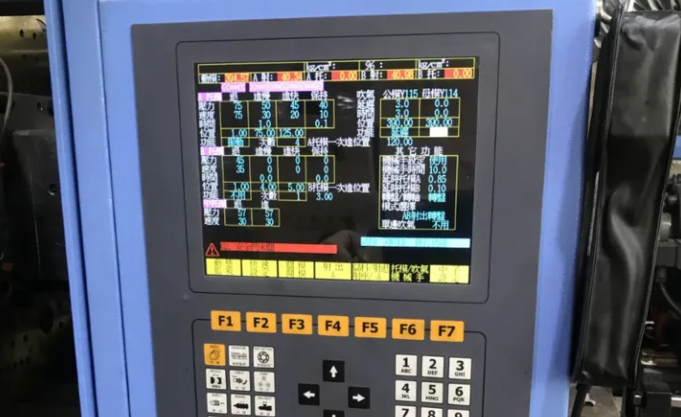
6. Mold temperature setting:
① If the mold temperature is set too low, the molten rubber flows in the mold cavity, the temperature drops faster, so the material flow resistance increases, so the pressure loss increases, increasing the internal stress and increasing the pressure in the mold cavity.
7. High mold temperature setting:
② Increase the crystallinity of molded products and more uniform structure, reduce the residual internal stress, deformation and improve the strength, reduce the resistance to flow of the material when filling, reduce the pressure loss, so that the product appearance of good gloss, but prone to burr, increase the near gate part and reduce the far gate part of the depression, so that the bonding line becomes smaller, increase the cooling time.
If you have mold customization needs, please contact us!
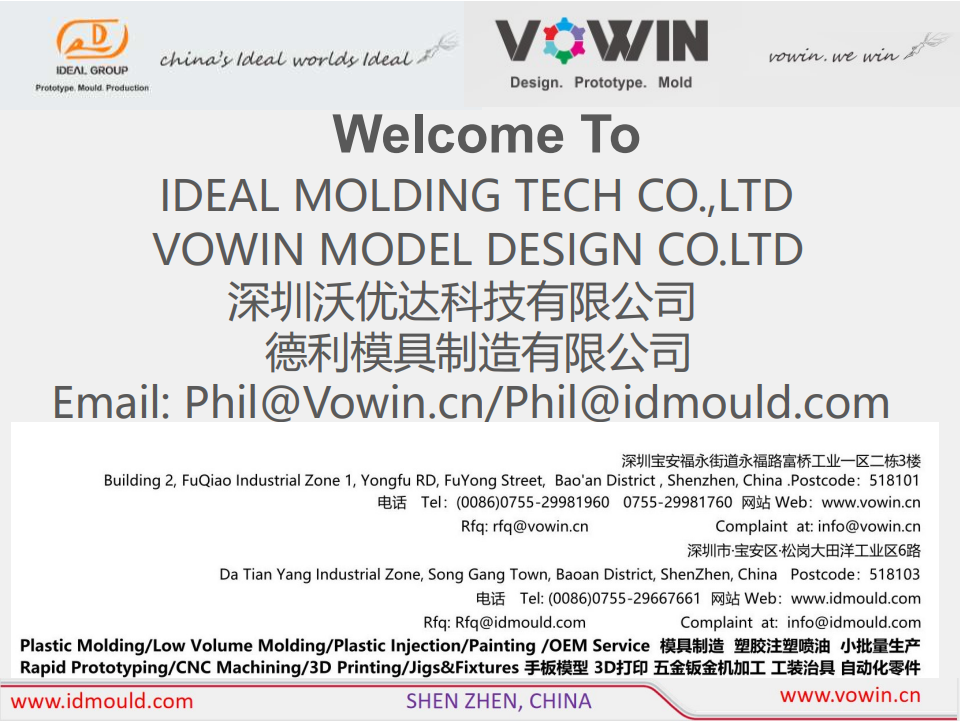
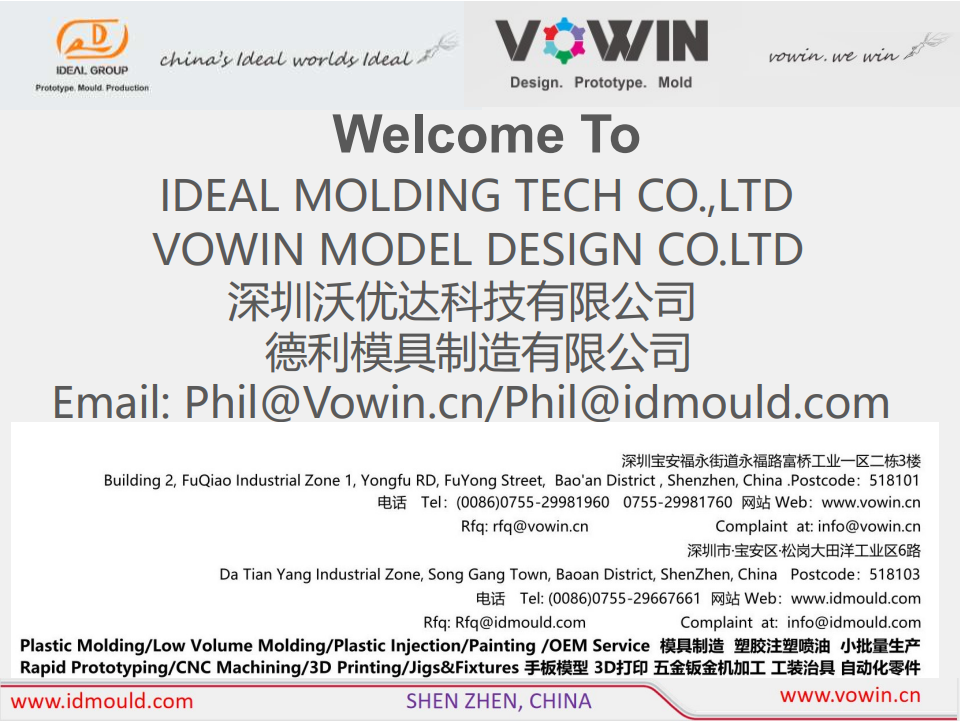
Posts by Topic
Recent Posts
- What kinds of plastic mold materials?
- What is the process of mold manufacturing?
- What should be paid attention to the polishing of injection molds?
- What is easy to ignore when maintaining and overhauling injection molds?
- What are the 6 systems of plastic molds?
- What are the methods of strengthening the surface of injection molds?
- What are the methods of insulation for injection molds?
- How to solve the problem of injection mold release difficulty?
- How can we increase the brightness of ABS injection molded parts?
- What are the common problems of mold maintenance and how to solve them?(1)