Resources
Automotive stamping die in large, precision and other areas of progress is obvious, the rapid development of plastic and rubber molds
Release time:2023-09-18
Automotive stamping die in large, precision and other areas of progress is obvious, the rapid development of plastic and rubber molds
The narrow sense of the automobile mold is punching the car body all the stamping parts of the mold in general, that is, "auto body stamping die", such as roof flap mold, beam reinforcement plate compression mold, etc.; broadly speaking, the "automobile mold" is the manufacture of automobiles on the molds of all the parts of the general term, such as stamping molds, injection molds, forging molds, casting wax molds, glass molds and so on.
1. China mold industry development history
China's mold manufacturing industry has roughly experienced four stages:
Start-up phase (1950s-1970s):The stage of the development of the mold manufacturing industry is relatively slow, mold manufacturing pure tail dependent on the manufacturer's parts processing workshop, mold varieties are relatively single, the mold is only for the manufacturer to produce white there are parts and components to use, mold manufacturing has not formed industrialization, commercialization and socialization.
Development phase (1980s):Benefit from the reform and opening-up policy and the rapid development of the manufacturing industry, mold manufacturing industry to attract a large number of private capital to enter. At the same time, with the restructuring of state-owned enterprises continue to promote, the traditional mold manufacturing enterprises gradually from the original "all-purpose mold factory" or "product factory mold workshop, group" mode gradually transformed into a specific industry or specific product services for professional mold enterprises. The stage of China's mold manufacturing industry towards specialized production.
Rapid development phase (1990s):Domestic mold manufacturing enterprises through the continuous introduction, digestion, absorption and re-innovation, rapid promotion of mold industry, technological innovation, product upgrading and industrial development. China's mold manufacturing industry has been gradually established, including mold research and development, production and sales of modern mold industrial system, the realization of the mold from the auxiliary tools to the equipment manufacturing industry, an important part of the transformation!
Competitive phase (early twentieth century to present):Domestic mold small and medium-sized manufacturers of serious product homogenization, a large number of foreign mold manufacturers with technological advantages began to influx into the Chinese mold market, intensifying the competition in the domestic mold market, some of the strength of China's local manufacturers began to focus on brand promotion, product innovation, service enhancement and channel terminal construction, and gradually open up the middle and high full of the mold market, in addition, downstream market presents a diverse range of needs, downstream customer awareness of the brand has also been gradually improved, China's mold manufacturing industry to enter the fast track of the development of the competition to the brand as a mainstay.
2. China's automotive mold industry development status
(1) Automotive stamping dies have made significant progress in areas such as large-scale and precision
① Mold enterprises have been fully applied to high-speed five-axis processing technology, full-process CAE and mold surface pressure gap processing technology, laser and medium-frequency surface strengthening technology and other advanced technologies. Leading mold enterprises use intensive, collaborative development of C-class car cover molds, especially high-strength steel, ultra-high-strength steel, all-aluminum body mold R & D and manufacturing technology has gradually matured.
1. China mold industry development history
China's mold manufacturing industry has roughly experienced four stages:
Start-up phase (1950s-1970s):The stage of the development of the mold manufacturing industry is relatively slow, mold manufacturing pure tail dependent on the manufacturer's parts processing workshop, mold varieties are relatively single, the mold is only for the manufacturer to produce white there are parts and components to use, mold manufacturing has not formed industrialization, commercialization and socialization.
Development phase (1980s):Benefit from the reform and opening-up policy and the rapid development of the manufacturing industry, mold manufacturing industry to attract a large number of private capital to enter. At the same time, with the restructuring of state-owned enterprises continue to promote, the traditional mold manufacturing enterprises gradually from the original "all-purpose mold factory" or "product factory mold workshop, group" mode gradually transformed into a specific industry or specific product services for professional mold enterprises. The stage of China's mold manufacturing industry towards specialized production.
Rapid development phase (1990s):Domestic mold manufacturing enterprises through the continuous introduction, digestion, absorption and re-innovation, rapid promotion of mold industry, technological innovation, product upgrading and industrial development. China's mold manufacturing industry has been gradually established, including mold research and development, production and sales of modern mold industrial system, the realization of the mold from the auxiliary tools to the equipment manufacturing industry, an important part of the transformation!
Competitive phase (early twentieth century to present):Domestic mold small and medium-sized manufacturers of serious product homogenization, a large number of foreign mold manufacturers with technological advantages began to influx into the Chinese mold market, intensifying the competition in the domestic mold market, some of the strength of China's local manufacturers began to focus on brand promotion, product innovation, service enhancement and channel terminal construction, and gradually open up the middle and high full of the mold market, in addition, downstream market presents a diverse range of needs, downstream customer awareness of the brand has also been gradually improved, China's mold manufacturing industry to enter the fast track of the development of the competition to the brand as a mainstay.
2. China's automotive mold industry development status
(1) Automotive stamping dies have made significant progress in areas such as large-scale and precision
① Mold enterprises have been fully applied to high-speed five-axis processing technology, full-process CAE and mold surface pressure gap processing technology, laser and medium-frequency surface strengthening technology and other advanced technologies. Leading mold enterprises use intensive, collaborative development of C-class car cover molds, especially high-strength steel, ultra-high-strength steel, all-aluminum body mold R & D and manufacturing technology has gradually matured.
With the development of automobile lightweight, pure aluminum and aluminum-magnesium alloy, carbon fiber and other new materials began to be used in electric vehicles and passenger cars in large quantities, especially aluminum-magnesium alloy, the third generation of high-strength steel, plastics, composites, sandwich materials forming die research and development, to the design and manufacture of automobile body molds to bring about new developments to speed up and enhance the level and quality of mold manufacturing. Above the mid-range car full set of cover parts mold, loaded in the stamping automatic line of intelligent molds, single set of weight up to 100 tons of ultra-large complex stamping die has been in the key backbone of the mold enterprise manufacturing.
In addition, the auto body mold enterprises to specialization, refinement, integration, intensification, industrial chain development, such as mold inspection folder integration, the main frame of the main frame of the integration of the development of technology, to achieve for domestic and foreign A/B class and part of the C-class passenger cars to provide mold forming integrated production line, to the industrial chain supply of the integrated complete set of molding line supporting the automobile OEMs, replacing the import of the body molding line in the extension of the industrial chain progress is obvious. It has made obvious progress in extending the industrial chain.
② The technical level of precision, large-sized molds and multi-functional high-efficiency molds is constantly improving. China's mold processing accuracy can reach 0.1μm, thin strip carbide progressive die life has reached more than 400 million times, has been able to produce more than 100 tons of ultra-large plastic molds, more than 3,000 times / min of high-speed stamping with multi-position progressive die and so on. Large auto parts progressive die technology is becoming more mature, high speed and high reliability has become an important feature of precision progressive die. With the demand for parts of increasingly large size and complex shape, it marks that the technology of large progressive die has entered into a mature stage. Thick plate precision punching composite forming die technology (represented by automotive seat adjuster, automotive transmission case forming die), thin plate high-speed stamping (such as new energy vehicle battery core structural parts) has become an important area for mold manufacturing enterprises to be competitive. Ultra-large forming parts as well as small ultra-precision parts of the mold design and manufacturing technology has become a hot spot for mold companies.
(2) Rapid development of automotive plastic and rubber molds
In order to enhance the international competitiveness of the mold, some of the domestic large-scale mold enterprises have focused on new technologies, new structures, new products, and has mastered the single-cavity, two-color automotive mold technology, deep-cavity products, low-pressure injection molding technology, automotive front-end module mold mold mold molding technology, plastic-coated steel mold molding technology, injection compression mold technology, multi-layer co-extruded blow mold technology for automotive fuel tanks, with a complete range of composite mold high-end mold design, development and production and manufacturing capabilities. We have complete design, development and manufacturing capability of composite molding high-end molds.
① Diversification of automotive interior and exterior trim and lamp injection molds. During the "13th Five-Year Plan" period, mold new products, new technologies, new processes continue to emerge, automotive ventilation grille and front bumper integrated mold injection mold, automotive air filter tube integrated mold injection mold, instrument panels and airbags integrated mold injection molds and other plastic molds have been widely to meet China's manufacturing industry, multi-color and multi-cavity injection molds, plastic silicone Multi-color and multi-cavity injection molds, plastic-silicone molding integration molds, rapid cooling and rapid heating molds, as well as functional molds for large inserts and 3D printed inserts with high-gloss requirements have been successfully researched and developed, and are supporting the diversified needs of the new automotive consumers. Light guide bar molds have been successfully used in the new models of Ford, Volkswagen and other international brands, realizing the localization of light guide bar molds, headlamp lampshade two-color molds, tail lamp three-color three-station molds have also been localized.
② automotive rubber mold technology level. Automotive rubber tire molds from the development of the two halves of the mold to the live mode, from the development of oblique rubber tire mold to radial tire molds, from the development of casting to inlay molds and all-steel molds, from the introduction of technology to the development of their own successful road. By the end of the "13th Five-Year Plan", some of the domestic production of all-steel radial rubber tire lubrication mold has reached or close to the international level. Glass covered rubber integrated forming mold, sealing rubber multi-cavity molds have been widely used.
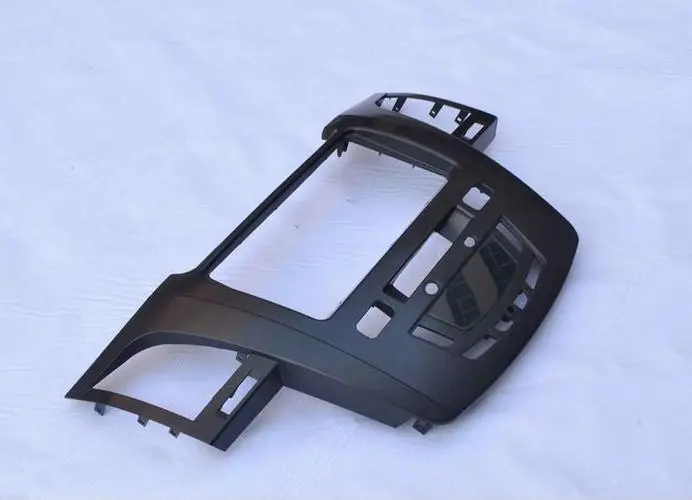
(3) die-casting molds, forging molds rich products
In the automobile mold, China's body stamping molds, interior and exterior plastic molds, automotive rubber tire molds, as well as large-scale complex die-casting molds, forging molds, has been in China to meet the needs of the mold market at the same time to the world, in the world has a very high cost-effective.
① die-casting mold technology continues to develop. Into the 21st century, with the automobile engine system, transmission system, suspension system, and even body structure parts and chassis structure parts gradually realized by the ferrous metal to casting non-ferrous metal transformation, die-casting mold into a high-speed development of the golden period. During the "thirteenth five-year" period, high vacuum die casting mold and extrusion casting mold and other light alloy die casting mold technology development at a high speed, and strongly promote the electronics, aviation, aerospace, construction and other industries mold parts forming development. With the development of new energy vehicles, also to motor, battery, electronic control and so on "three electric" die casting mold has brought a new technology revolution. Low-pressure casting mold, differential pressure casting mold technology has also been developed.
② forging mold to achieve domestic self-matching. Front axle, crankshaft, pin rail, scraper, steering knuckle and other large-scale machine forging die and hammer forging die, as well as small and medium-sized machine forging die and hammer forging die, such as connecting rods, linkage, small crankshaft, piston, hot heading machine molds and so on have become an important part of the automobile mold, forging die completely realize the domestic self-matching.
3. Industry competition pattern
(1) International competition
From a global perspective, technologically leading mold enterprises are mainly concentrated in Germany, Japan, the United States and other industrially developed countries. These countries have a perfect technology research and development platform and personnel training system, in the design concept, process technology, research and development experience, there is a clear leading edge, the industry focuses on specialized positioning, specialized division of labor and the development of industrial chain synergies, the production of molds with a long service life, quality reliability and stability, manufacturing precision and standardization of the high degree of characteristics. However, in the context of specialization and global procurement, consider labor costs, close to market demand and other factors, some mold enterprises will gradually transfer the production of mold to developing countries in order to continuously enhance its market competitiveness.
China's mold industry in terms of market size has reached the forefront of the world, but the industry enterprises in business management, production capacity, product quality and other aspects of the world's leading level compared to the gap still exists. In recent years, with the gradual improvement of China's industrial system, China's mold design and production process level and the gap between foreign developed countries continue to narrow, mold development cycle, market response time, production costs and other aspects of a greater enhancement. In specific segments, some of the industry's leading companies can participate in the synchronized research and development of downstream customers, the competitiveness of the international market has gradually increased.
(2) Domestic Competition
Benefit from the transfer of global manufacturing, China's mold industry in recent years to achieve rapid development, has become the world's mold production and trade in large countries, but with the transformation and upgrading of the manufacturing industry on the demand for mold and the international equipment manufacturing industry, compared with the advanced level of development, China's mold industry is still in the "big but not strong" stage. Mold production enterprises and general industrial products enterprises, compared with the number of enterprises, the overall scale of individual enterprises is small, mostly small and medium-sized enterprises, concentration is low.
Domestic mold industry marketization is high, the competition is more intense, the domestic mold manufacturing enterprises from the mode of operation can be roughly divided into four categories:
① The first category is the product group investment in the establishment of the mold company, mainly for the production of products belonging to the group and new product development services, most of the use of divisions, branches of the way to run. This type of mold companies continue to improve the mold design and manufacturing technology and manufacturing capacity to meet the group's product competitiveness to improve demand.
② The second category is a clear market segmentation of the positioning of large-scale mold enterprises (such as automotive parts, rubber tires, motor cores, mold standard parts, etc.), the mode of operation, including shareholding (including listed companies), limited liability company, sole proprietorships and so on. This type of mold enterprises in investment management, business management, technological innovation, talent development, brand building and other aspects of the continuous all-round improvement to maintain the competitive advantage of enterprises, is the backbone of China's mold manufacturing industry.
③ The third category is to mold niche positioning of small and medium-sized mold enterprises (such as precision injection molds, multi-position progressive punching die, metal extrusion mold, plastic extrusion molds, checking, jigs and fixtures, etc.), the mode of operation, including joint ventures, sole proprietorships, individuals, and so on. This kind of mold enterprises in the market mostly focus on the global and actively track the development of new industries and mold forming new technologies, the use of their own formation of niche areas of "specialization, precision" advantage, to make up for the first, the second type of enterprise "ability gap" at the same time, timely detection of And quickly seize the new mold market, is to promote China's mold industry "from big to strong" of the vital forces.
The fourth category is based on the agreement to manufacture (OEM), commissioned processing of small molds and parts processing enterprises, operating in a flexible manner, such as partnerships, families, individuals, etc.. This type of mold enterprises focus on the mold industry cluster area in the development of professional mold enterprises on the demand for social processing capacity, and commissioned enterprises to establish mutual trust and complementary cooperative relationship, to become a part of the "mold manufacturing ecosystem". Mold industry has obvious "Matthew effect". Sufficient funds, large-scale mass production, advanced equipment, research and development capabilities of the first and second type of excellent manufacturers with long-term technical research, experience and product quality advantages of the strength of the trust of large customers, and customers to establish an interdependent co-development of the strategic partnership, and continue to obtain orders from large customers, with the business scale continues to expand, the customer base increased, the increase in corporate profitability, the class of enterprises to continue to increase R & D, equipment investment, and become part of the "mold manufacturing ecosystem". Enterprises continue to increase R & D, equipment investment, so that their own technical capabilities, manufacturing capacity to continue to improve the competitive strength of the more and more. The capacity and varieties can not meet the different needs of customers, technology research and development capabilities are weak, unable to improve technology and product standardization and reduce production costs, product consistency is low, often due to a lack of funds, insufficient orders, meager profits can not support the follow-up technology, equipment investment, resulting in weaker and weaker competitiveness, which presents "the stronger the stronger the weaker the weaker" polarization. The weaker the weaker" polarization pattern.
4. automotive mold industry development trend
(1) automotive mold to precision, large-scale, automation and intelligent direction of development
In terms of precision, automobile vehicle consists of about 30,000 parts, the product structure is complex, high precision, and at the same time for the realization of automated welding, automated assembly, the processing accuracy of automotive parts and components required more and more, thus promoting the mold continues to develop in the direction of precision.
In terms of large-scale, stamping die, for example, in the past, automotive stamping die commonly used single-station die, multi-station die structure design, with technological advances and equipment level, can reduce costs and improve production efficiency of the smooth-feeding die in the production of metal structural parts have been more and more widely used. The continuous stamping process of the downstream feeding die makes the design of the die more complicated, and the volume and weight of the die increase. In the automation and intelligence of automotive mold, on the one hand, CAD, CAE and other intelligent design and engineering software in the mold design phase of the extensive use, on the other hand, embodied in the robot transfer technology, optical automatic detection technology in the mold production and assembly of a wide range of applications.
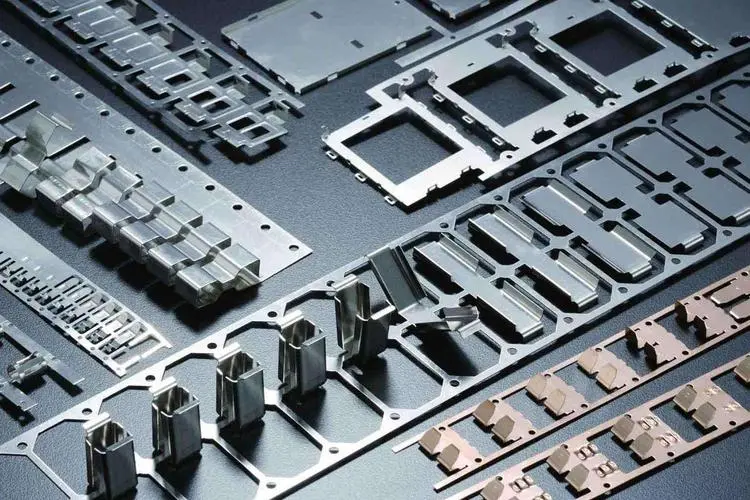
(2) the future of mold technology is mainly to the direction of new material molding technology development
Safety and energy saving and emission reduction is the eternal theme of automobile development. Most of the traditional automobile body covering parts using steel, without reducing the safety of the car under the premise of reducing the weight of the car, reduce energy consumption and carbon emissions, various automobile manufacturers continue to try to introduce a variety of lightweight, high-strength new materials, such as the use of high-strength steel plate, the use of galvanized sheet metal process. The realization of lightweight body has become a mainstream R & D direction in the design of automotive parts, which requires mold companies to study and explore the failure of new materials, failure mechanisms, failure laws and material categories, parameters of the qualitative and quantitative relationship between the development of the corresponding lightweight, high-strength materials, molding technology and mold design and manufacturing technology.
(3) mold development capabilities as the core, part of the automotive mold enterprise business gradually to the downstream parts industry expansion
Mold technology level determines the production yield of metal structural parts, production efficiency, material utilization. Stamping die industry, for example, part of the stamping die enterprises to excellent mold design capabilities as the core, play the role of metal structural components "performance amplifier", to provide customers with structural components process design, mold design and development, mold manufacturing, metal structural components production and sales of integrated services, a more efficient response to customer demand.
As the automotive stamping die is the downstream automotive metal structure parts production and manufacturing of basic equipment, mold manufacturers usually have a more in-depth understanding of the automotive metal structure parts of the market demand, process flow, sales channels, etc.. Within the industry, some of the automotive stamping die enterprises with stronger technical strength and higher management level have gradually extended to the downstream industry chain with the die as the core, established metal structural parts production lines, and provided customers with integrated services from dies to products based on the stamping dies designed and developed by themselves.
5. Industry barriers
(1) Customer Barriers
Automotive molds, as the basic equipment for auto parts production, will largely affect the quality, performance and service life of mass-produced parts, so downstream customers have very strict requirements for mold suppliers. Famous downstream enterprises usually formulate a set of strict standards to examine the ability of mold suppliers in various aspects, not only require suppliers to provide reliable quality products, but also on the supplier's R & D and testing capabilities, the advanced manufacturing equipment and maintenance status, processing technology, production process arrangements, experienced engineers, the quality and number of technicians, the implementation of the staff, quality management system, the working environment and other aspects of the strict requirements. Strict requirements are put forward in the following aspects. After the qualified inspection, it is still necessary to go through a number of project verification before the mold manufacturer will be included in its global procurement system to establish a long-term cooperative relationship. These downstream well-known enterprises once identified a mold supplier qualification, in order to ensure the consistency of product quality and delivery timeliness and reliability, usually will not easily interrupt the cooperative relationship, thus forming a strong customer adhesion. This strict supplier qualification, as well as based on long-term cooperation and the formation of stable customer relationships, new entrants to the industry to form a high customer barriers.
(2) Technical barriers
Automotive molds for customized products, complex structure, high precision requirements, personalized demand is obvious, the above characteristics of the mold requires mold manufacturing enterprises must have a strong product development capabilities, technological innovation level and cover the entire production cycle of quality assurance capabilities. At the same time, with the downstream enterprises on the mold material strength, service life, manufacturing accuracy, punching efficiency, plastic deformation characteristics of the plate, unequal material thickness, lightweight and other technical requirements continue to improve, the mold manufacturing enterprises of product development and manufacturing capacity to put forward higher requirements. Mold manufacturing enterprises in the manufacturing process, quality control, on-line commissioning and other aspects of the need for long-term practical experience and production applications in order to master the core technology, and through the continuous acceptance of orders to further optimize the original technology, through the continuous development of new products to meet the customer's new needs, followed by the formation of new processes, new methods. New entrants to the industry due to the small size, lack of experience, it is difficult to master the mold design and development capabilities and core production technology in a short period of time, the formation of technical barriers.
(3) Capital Barriers
Automotive mold industry has a large fixed investment, manufacturing and delivery cycle is longer, belongs to the capital-intensive industry. First of all, enterprises in the early stages of construction need to buy special processing equipment for the production of molds, the high stability and reliability of this type of equipment determines the high price level, the initial fixed asset capital investment is larger; Secondly, molds for customized products, manufacturers need to invest in pre-design research and development and core component procurement, design and development of advances in capital is generally higher; In addition, from the acquisition of orders to the design, processing, assembly, commissioning and other production links, and then to the shipment, the final sales payback link, the order cycle is generally higher. In addition, from order acquisition to design, processing, assembly, debugging and other production links, and then to the shipment, the final sales payback link, the order cycle is generally longer, the enterprise's production working capital needs are greater. With the intensification of competition in the mold industry, enterprises in technology, equipment, personnel and other aspects of the investment is growing, which requires companies to enter the industry has a strong financial strength.
(4) talent barriers
Automotive mold industry involves mechanical design, structural mechanics, materials science and other multidisciplinary and technical applications, is a technology-intensive industry. Mechanical design, the need for molds, assembly, stamping, welding and other technical processes for continuous optimization; structural mechanics, mold design and development links need to ensure that the material in the role of force, a specific deformation, while avoiding possible cracking or wrinkling. With the innovative use of processes, the accelerated pace of technological innovation, production automation and information technology to enhance the level of long-term cultivation of the mold industry to cultivate a group of deep professional background, rich practical experience, research and development and innovation capabilities of the outstanding technical talent team, to maintain a leading edge in the industry change. For new entrants in the automotive mold industry, especially the lack of scale advantage and production experience of enterprises, it is difficult to build a reasonable professional structure of the talent team in a short period of time and always ensure the stable development of the talent team, so the automotive mold industry there are certain barriers to talent.
If you have project requirements, please contact us!
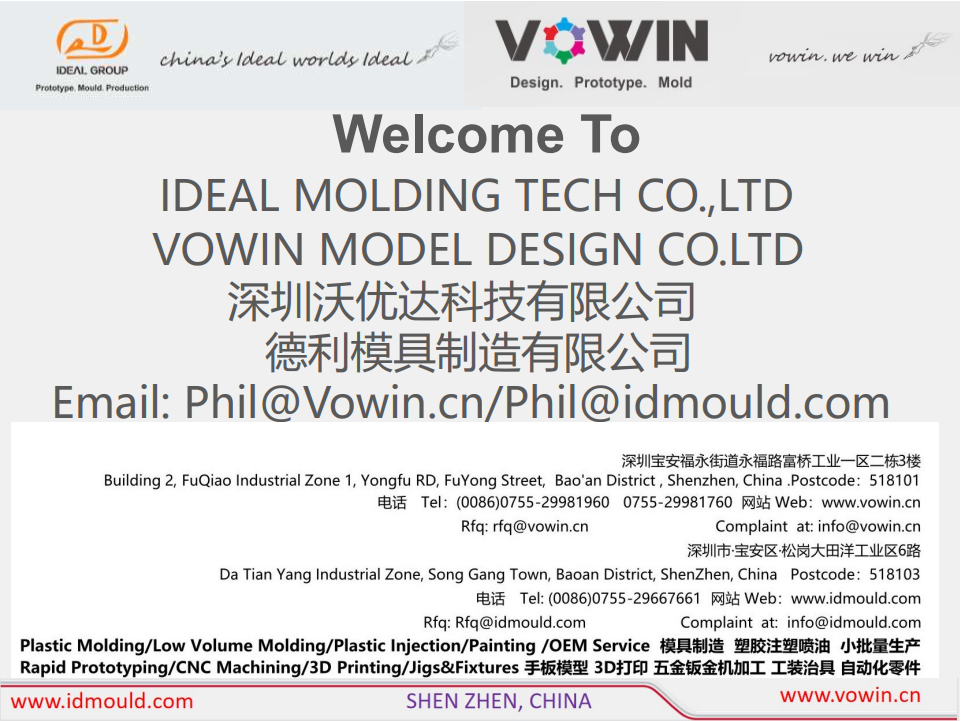
Posts by Topic
Recent Posts
- What affects injection mold machining accuracy and productivity?
- Shenzhen top five mold manufacturers: how plastic products are processed and produced?
- Shenzhen Ideal Vowin mold manufacturer: how to effectively improve the precision of mold processing?
- Chrome plating, a process that makes cars stylish
- What is automotive hot stamping and molding technology?
- What is the difference between a hot runner and a cold runner in the mold?
- Automotive stamping die in large, precision and other areas of progress is obvious, the rapid development of plastic and rubber molds
- The top ten problems that are likely to occur in the mold testing process