Resources
What is the difference between a hot runner and a cold runner in the mold?
Release time:2023-09-19
What is the difference between a hot runner and a cold runner in the mold?
Why are there hot runners and cold runners in the mold?
Runner is the basic form of injection mold. The so-called cold runner is a traditional injection mold. After injection, there is condensate in the runner that needs to be discharged!
With diminishing resources, increased competition in the marketplace, and significant increases in raw material prices, it is essential to make a big contribution to the issue of saving materials! This is also an important reason for the emergence of hot runner, it can be said that it is the inevitable product of the development of social industrialization.
The emergence of hot runner to solve the problem of resource waste and cost savings in the injection molding process has achieved great results. Hot runner has gradually developed into the main direction of the development of injection molding, and will be widely used.
However, due to the costing problem, there are many small and medium-sized molds have not yet applied hot runner! And there are some materials that must be injected into cold runner molds to achieve better control!
So now there are cold runners and hot runners in the injection mold industry!
Comparison of hot and cold runners
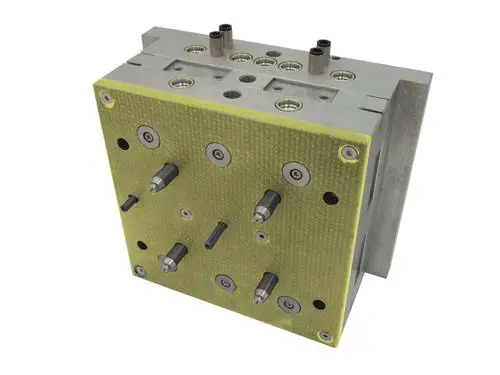
Comparison of hot and cold runners
Hot runner system began in the injection molding industry in the runnerless system, as an advanced plastic injection molding processing technology, the popularity of the application of developed countries in the West can be traced back to the middle of the 20th century or even earlier.
Hot runner has a lot of advantages, therefore, in foreign countries to develop faster, many plastic mold factory manufactured molds more than 50% of the use of hot runner technology, some mold factory even reached more than 80%. In China, this technology in the last decade to really get the full promotion and application, with the rapid development of the mold industry, the hot runner in the plastic mold using the proportion has gradually increased, but overall has not reached the proportion of overseas hot runner mold.
Why is there this kind of hot runner technology occurs? Hot runner technology and what benefits can bring us? Understanding of injection molding engineers know that the conventional injection molding process often have the following adverse conditions:
a. Tough to fill;
b.Easy deformation of thin-walled large products;
c.Consumption of raw material for sprue;
d. Inconsistent quality of injection molded parts in multi-core molds.
The occurrence of hot runner technology brings a more perfect solution to various problems. Generally speaking, the selection of hot runner has the following advantages:
1. Shorten cycle time
Because the runner system has no cooling time limit, parts can be ejected in a timely manner after molding and curing. The forming cycle time for many thin-walled parts produced with hot runner molds can be less than 5 seconds.
2. Save Plastic
Because there are no cold runners in a pure hot runner mold, there are no production costs. Hot runner technology is an effective way to reduce material cost and material cost.
3. Reduce scrap and improve product quality.
During the forming process of hot runner molds, the hot runner system provides accurate control of the temperature of the plastic melt. The plastic can flow into the cavity in a more uniform state, resulting in better quality
During the forming process of hot runner molds, the hot runner system provides accurate control of the temperature of the plastic melt. The plastic can flow into the cavity in a more uniform state, resulting in better quality
consistent parts. Hot runner molded parts have good gate quality, low residual stress after demolding and small deformation.
4. Production automation
Elimination of subsequent processes facilitates production automation. Finished products are formed by hot runner molds without the need for trimming gates and recycling cold runners. Favorable to production automation.
Compared with hot runner, the cold material produced by cold runner needs to be crushed and recycled again, but the mold design is simple and widely used.
5. Expand the application areas of injection molding process
Many advanced plastic molding process to be developed on the basis of hot runner technology. Such as PET pre-molding manufacturing, mixing colors in the mold co-injection, a variety of materials co-injection process, STACKMOLD (stacked box casting mold) and so on.
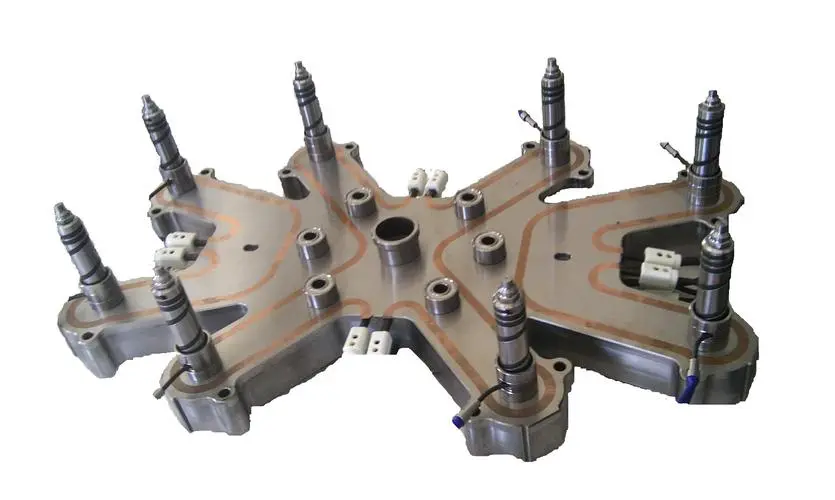
Although compared with cold runner molds, hot runner molds have many significant advantages, but mold customers also need to grasp the defects of hot runner molds. They are summarized as follows:
1. Higher mold costs
Hot runner components are more expensive, and hot runner mold costs may be significantly higher. If the part production is small, the mold tooling cost is high as a percentage of the cost, which is not economically viable. For many mold customers in developing countries, expensive hot runner systems are one of the main issues affecting the widespread use of hot runner molds.
2. hot runner mold production process technology requirements are high
Hot runner mold must be precision machining machinery as a guarantee. Hot runner system and mold integration and coordination requirements are extremely strict, otherwise the mold in the production process will appear a lot of serious problems.
3. Complicated operation and maintenance
Compared with the cold runner mold, hot runner mold operation and maintenance complicated. If the application operation error is very easy to destroy the hot runner parts, so that the production can not be carried out, resulting in great property losses. For new users of hot runner molds, it takes a long time to accumulate application experience.
Components of a Hot Runner System
Although there are many hot runner manufacturers and a wide variety of hot runner product lines worldwide, a typical hot runner system consists of the following major components: hot runner plates, nozzles, temperature controllers, and ancillary parts.
A successful hot runner mold application project requires multiple stages to ensure success. One of the more important are two technical elements: one is the control of plastic temperature; the second is the control of plastic flow characteristics.
1. Control of plastic temperature
In the hot runner mold application of plastic temperature control is extremely important. A lot of production process and commodity quality problems arise directly from the hot runner system temperature control is not good. Such as the application of torpedo type hot nozzle gate injection molding process when the poor quality of goods gate problems, valve type hot nozzle molding valve needle completely off the difficult problem and its multi-cavity mold parts filling time and quality inconsistent problems. If possible, should try to choose the hot runner system with multi-region segmented temperature control, in order to increase the flexibility of use and communication capabilities.
2. Control of plastic flow
Plastic flow should be balanced in the hot runner system. The gate should be opened at the same time to synchronize the plastic filling of each cavity. For the net weight of the part is too big difference to carry out the sprue specification design equalization. Otherwise, it will happen that some parts are not enough to fill the mold holding pressure, but some parts are too much to fill the mold holding pressure, burrs are too big and quality is poor and other problems. Hot runner sprue specification design should be reasonable. Size is too small mold filling pressure loss is too large. Size is too large hot runner volume is too large, the plastic in the hot runner system retention time is too long, damage to the material properties and cause the parts after molding can not meet the application requirements.
A few things to keep in mind when designing a hot runner mold
(1) Because of the severe thermal expansion that occurs after heating, it is important to leave enough space for expansion between the hot runner system and the mold.
(2) Large contact areas between the hot runner system and the mold should be avoided as much as possible.
(3) Because of the severe heat loss, a thermal pad should be added between the mold and the injection molding machine to reduce heat loss. The insulation board must be insulating material, commonly used are bakelite board, various plastic sheets or fiberglass.
If you have a project requirement, please contact us!
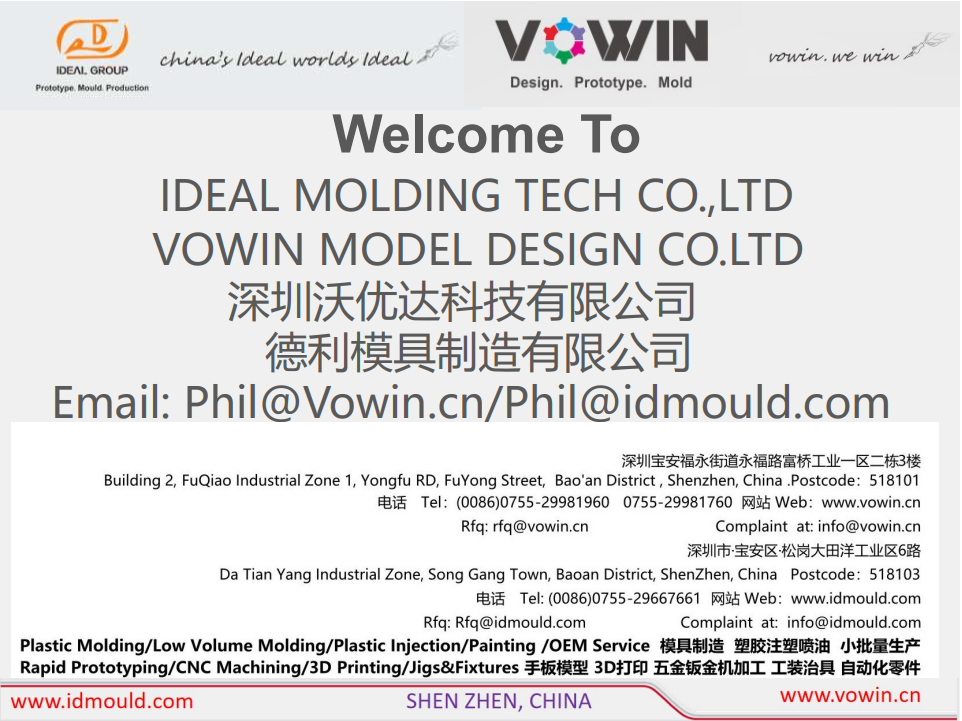
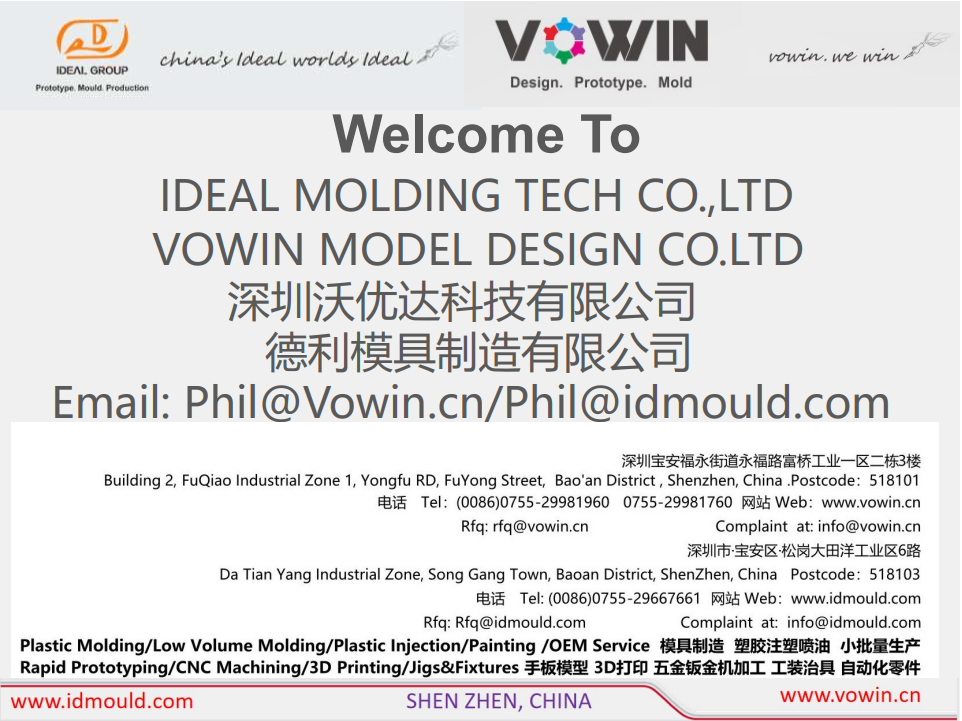
Posts by Topic
Recent Posts
- What affects injection mold machining accuracy and productivity?
- Shenzhen top five mold manufacturers: how plastic products are processed and produced?
- Shenzhen Ideal Vowin mold manufacturer: how to effectively improve the precision of mold processing?
- Chrome plating, a process that makes cars stylish
- What is automotive hot stamping and molding technology?
- What is the difference between a hot runner and a cold runner in the mold?
- Automotive stamping die in large, precision and other areas of progress is obvious, the rapid development of plastic and rubber molds
- The top ten problems that are likely to occur in the mold testing process