Resources
Hot Runner Temperature Control: A Low-Investment Solution for Challenging Molding
To understand the importance of hot runner controls, you need to examine how they actually control temperature, processing implications and mold design considerations.
Improved hot runner temperature control can provide a competitive advantage. Consumers have an unending appetite for new products. These products will be supplied by companies that excel at understanding their niche customers and delivering them the products they want. Therefore, the motivation of successful companies is to serve their customers, not the existing supply chains.
Whether you are a proprietary or custom molder, processing advancements are critically important to the future competitiveness of the injection molding industry and your organizations. With them you will be able to alter your business model, select more profitable markets and improve performance in existing markets. This article will review how improved hot runner temperature control will help you achieve these processing advancements.
Market Drivers
Molders have been making due with existing injection molding machines and auxiliary equipment for several years. They also are buying on the used market now more than ever. The American Plastics Council documents that consumption of the most widely used resins have remained flat. Meanwhile, resin price has more than doubled in the last 10 years. This means that injection molders are converting similar amounts of plastics while trying to keep up with changing consumer preferences. They are challenged to use older equipment and deal with high material costs.
Processing Implications
There are many significant problems that arise. First, designers are demanding extremes of size, shape, dimensional tolerance and surface characteristics in order to provide consumers with the products they want. Using older equipment often means that it was originally specialized for something else or was relatively generic. The implications are less flexibility on the resins used, longer cycle times and less than optimal operations scheduling, staffing and managerial support. Finally, a less than optimal molding cell causes imbalance and inefficiency in the entire facility—including cooling water, electrical consumption and lower overall throughput, especially where molding is one of many links in the production chain.
Considering today’s molding challenges, improving hot runner temperature control now offers a significant opportunity to drastically improve results at a relatively low investment compared to other auxiliary and primary equipment.
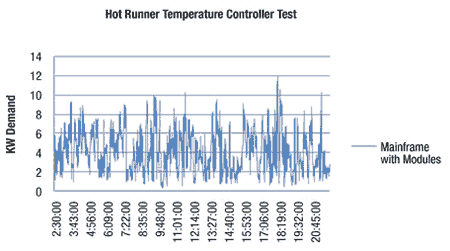
Figure 1. Traditional hot runner temperature controller that is comprised of a main power supply cabinet within which are many independently controlled modules. Figures courtesy of Fast Heat.
Specifically, hot runner temperature control affects finished part quality. Figure 1 shows a traditional hot runner temperature controller that is comprised of a main power supply cabinet within which are many independently controlled modules. A power energy audit monitor was used to document KW Demand of the incoming power to the cabinet. This molding cell was not operating well due to burnt material and inconsistent part weight. It was a significant burden and distraction to the processors and production managers.
A similar test was performed by Florida Power and Light. In this case the controller was a more advanced system using a computerized processor and interface. However, due to independent zone control and the inability to predict optimal power supply, this controller caused a 12 percent further deviation on the mean internal dimension for an intravenous medical device than a more advanced controller.
The implications of using a temperature controller with independent zone control and without predictive capabilities are variations in all of the other plastic variables: flow, pressure and time. As each one of these variables fluctuates they cause additional variation in each of the others. The end result is a process that makes molding more difficult. It also is important to note that temperature has a much more significant impact on flow than the other variables.
Mold Design Considerations
New part challenges directly translate into new tooling challenges. While many hot runner system suppliers have responded with new designs, there are always new processing challenges and learning curves to navigate. This includes the design, location and consistency of heaters, thermocouples, flow channels, gate tips, water channels, manifolds and plates. Figure 2 shows some of the ways hot runner design affects plastic variables.
Figure 2 | |
Plastic Variable | Hot Runner Contribution |
Temperature | • Heater Specification & Quality |
• Thermocouple Location & Quality |
|
• Shear from Geometry & Surface Quality | |
• Heat Losses from HR design | |
Flow Rate | • Plastic Temperature |
• Channel Length & Diameter | |
• Tip Geometry | |
• Surface Detail | |
Pressure | • Plastic Temperature |
• Channel Length & Diameter | |
• Tip Geometry | |
• Surface Detail | |
Time | • Plastic Temperature |
Ways hot runner design affects plastic variables. |
Some basics to consider when evaluating your hot runner system design are:
- Are any of the manifold flow channels directly crossing perpendicular underneath a tubular heater? These can cause burning.
- Are any of the manifold thermocouples placed directly opposite of each other? These can cause zones to provide false feedback.
- Are the thermocouples on the nozzles optimally located for the nozzle’s heat profile? They should be at a point of stable heat loss.
- Do all nozzles have a thermocouple? This provides optimal system control when using the proper type of hot runner controller.
- Is the entire system thermally balanced and managed with proper water channel size and location?
- Have the gate geometries been proven on similar materials, parts and mold configurations?
Once these basics are in place, you will be able to learn the nuances of your new hot runner and mold design. Keep in mind that all of these factors can be negatively exaggerated, positively compensated for or just left to do their job by the hot runner temperature controller.
Compensating for Challenging Part Designs, Older Equipment and High Resin Costs
The solution is a hot runner temperature controller that manages all zones as a complete system while predicting temperature behavior. Specifically, a single zone cannot operate by itself, but only in consideration for how it affects the entire system. Secondly, zones must be monitored more often than they respond. If zones simply respond every time there is a call for power, it will create volatility within the zone and within the system as seen in Figure 1. The controller should instead predict and react to trends. This will ensure the least amount of disturbance to the plastic as it travels through the hot runner system and causes the least amount of variation build-up as described earlier under Processing Implications.
Consider the problem application depicted earlier. In Figure 3 the red line represents this solution. It is smooth and at a much lower overall KW demand. The molder in this case alleviated their previous burning and inconsistent part weight problems.
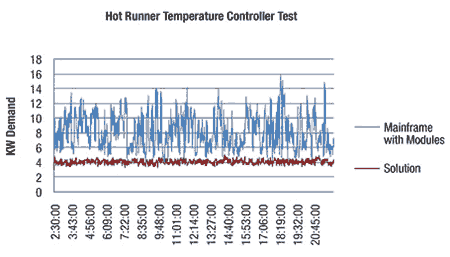
Figure 3. Hot runner temperature controller that manages all zones as a complete system while predicting temperature behavior.
The type of hot runner temperature control in Figure 3 can give your company a competitive advantage. Specifically, it offers the following benefits:
- Makes it possible to mold more challenging parts.
- Compensates for used equipment’s lack of specialization and precision.
- Reduces scrap.
- Predictable schedule utilization and higher overall throughput.
- Lower labor and managerial costs.
- Efficient electrical and cooling systems.
- Allows alternative resins to be used. This is a game changing opportunity.
Selection Criteria
Below is a list of considerations when selecting a hot runner temperature controller:
- Does the controller supply power to zones individually or in consideration of the entire system? It should consider the entire system.
- Does the controller read each zone many times before responding and then respond to a predicted trend? It should have predictive capability.
- Is the controller easy for all users to learn and operate? Are all functions used or only those easily found and understood? We believe all functions should easily be learned and used with a simple start-up guide.
- Does the controller automatically detect and alarm mold problems or must you initiate the process? We believe automatic, real time response is safer and more reliable.
- Does the controller offer molding cell integration to prevent cold shooting, tool damage, leakage and unforeseen heater failure? Can all alarms be sent from the controller? Can the controller be remotely turned on, off, boost or idled?
- Can the controller be stored in any position away from critical floor space?
- If you require transformers, how compact is the matching transformer?
- Is the controller completely modular and accessible without tools?
- Is the controller customizable to maximize the benefit for your application?
- Is the controller easily made available for demo applications to test its performance?
related catagory Hot Runner
- What affects injection mold machining accuracy and productivity?
- Shenzhen top five mold manufacturers: how plastic products are processed and produced?
- Shenzhen Ideal Vowin mold manufacturer: how to effectively improve the precision of mold processing?
- Chrome plating, a process that makes cars stylish
- Six injection molding processing technologies for home appliance plastic products
- Advantages and disadvantages of injection molding vs blow molding
- What is automotive hot stamping and molding technology?
- What is the difference between a hot runner and a cold runner in the mold?
- Automotive stamping die in large, precision and other areas of progress is obvious, the rapid development of plastic and rubber molds
- The top ten problems that are likely to occur in the mold testing process