Resources
What are the process standards for machining mold parts such as mold nuts, inserts, tilt tops, sliders, etc. for injection molding production?
Release time:2023-11-29
What are the process standards for machining mold parts such as mold nuts, inserts, tilt tops, sliders, etc. for injection molding production?
In order to ensure the rationality and consistency of the mold making and processing process, optimize the processing process, and improve the progress of mold making, each mold factory will generally formulate a process standard suitable for this factory. This article provides a standard for reference.
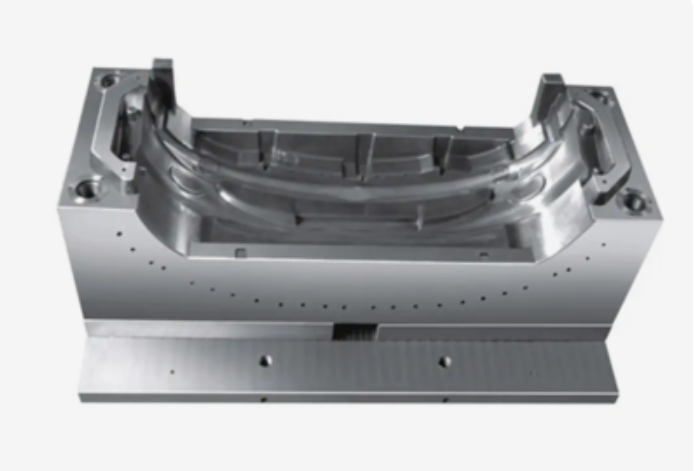
I. Craftsman compiling process card
Craftsman compiling process card should be detailed in the process card to indicate the amount of machining reserve, the orientation of the reserve, roughness requirements and precautions.
Processing process card preparation principles: in the premise of being able to ensure accuracy and quality, give priority to the use of equipment with high processing efficiency. The processing efficiency of milling machine, CNC, grinding machine is faster than that of wire-cutting and electric pulse, especially the slowest processing efficiency of electric pulse. The dimensions on the drawings cannot be changed at will (only the technician can change them).
II. Principle of machining allowance
Need heat treatment processing of the workpiece, heat treatment before the shape of the preparation size of one side plus 0.25mm grinding allowance, mold nuts, inserts need CNC rough machining of the part, one side of the allowance 0.2mm, clamp milling machine rough milling shape of one side of the allowance 0.3-0.5mm, wire cutting after the need for grinder processing of the workpiece, molding part of one side of the allowance 0.05mm, shape of the rough one side of the allowance 0.1mm The grinding allowance of 0.1mm is reserved for one side of the shape roughing; After CNC finishing and electric pulse, the workpiece should be mirror polished, and the polishing allowance of 0.03mm is reserved for one side of the workpiece.
III. Processing accuracy requirements
The manufacturing accuracy of the mold size should be within 0.005 ~ 0.02mm; verticality requirements in the range of 0.01 ~ 0.02mm; coaxiality requirements in the range of 0.01 ~ 0.03mm; moving, fixed mold parting surface of the two planes of the parallelism requirements in the range of 0.01 ~ 0.03mm.
After closing the mold, the gap between the parting surfaces is less than the overflow value of the molded plastic. The rest of the template with the parallelism of the surface requirements in the range of 0.01 ~ 0.02mm; fixed part of the general selection of the accuracy of the fit within the range of 0.01 ~ 0.02mm; small cores if there is no requirement for insertion or the size of the impact of the small can be taken to the bilateral 0.01 ~ 0.02mm gap fit; sliding part of the general selection of the accuracy of the fit H7/e6, H7/f7, H7/g6 three kinds of.
Note: Mirror, such as those who have made a dependency step of the inserts, with can not be too tight, otherwise in the inserts from the front to the back when knocking, used to knock the tool is easy to touch the mirror, such as not affecting the size of the product, can be taken as a bilateral 0.01 ~ 0.02mm clearance with.
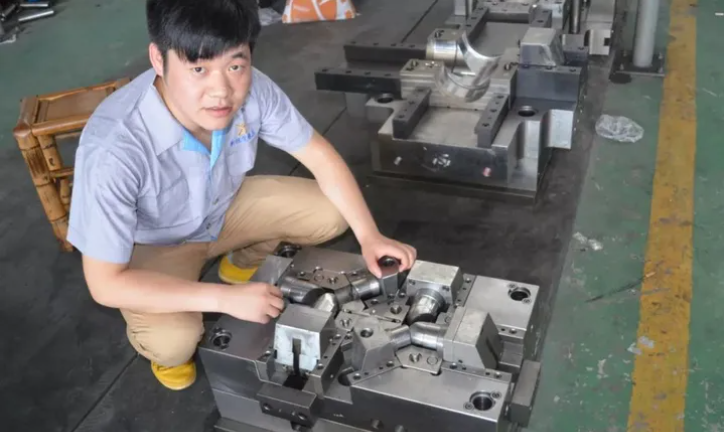
IV. The principle of CNC dismantling electrode
Mold cavity core should be removed first appearance of the main electrode, and then remove the other main electrode, and finally remove the local electrode; fixed mold appearance electrode should be considered as a whole processing, the CNC clearing angle can not be used to clear the angle of the line cutting, so that the appearance of the fixed mold surface is complete, no joint marks; the depth of the moving mold is not a big difference in the reinforcing bars, bars, columns can be processed together as far as possible to do in an electrode; deeper bars to do inserts, to be done individually! Electrode side hit, in order to prevent the accumulation of carbon when the electric pulse; dynamic mold electrode try not to CNC milling after a good but also wire cutting clear angle, such as to, the electrode should be broken down and disassembled or directly using wire cutting; dynamic mold of the tendon part and the bar bit or column spacing more than 35mm, it should be separated to do, saving copper.
Large electrode roughing spark bit to do unilateral 0.3mm, finishing spark bit to do unilateral 0.15mm; general electrode roughing spark bit to do unilateral 0.2mm, finishing spark bit to do unilateral 0.1mm; small electrode roughing spark bit to do unilateral 0.15mm, finishing spark bit to do unilateral 0.07mm.
V. CNC machining principle
Mold nuts, inserts need CNC roughing part, one side of the margin reserved 0.2mm, heat treatment needs CNC finishing workpiece, if the product appearance allows, CNC can be finished in place of the mold cavity core, priority CNC machining, such as can not be processed in place to do the electrode, with electric pulse processing.
VI. Dynamic and static mold kernel processing technology
(1) Prepare materials;
(2) milling machine processing: drilling water transport holes (water transport holes plug deepest distance from the lateral water transport holes 3-4mm), threading holes, drilling, tapping screw holes, drilling, reaming thimble holes, mold numbering, datum angle, hanging table to give way;
(3) CNC machining: rough machining;
(4) Heat treatment processing: specify the hardness requirements;
(5) Grinding machine processing: grinding six-sided angle ruler, shape to match the frame size grinding standard (if the mold is a piece of the external dimensions than the size of the drawing of the negative 0.03mm-0.05mm, if the mold is a piece of two pieces of the mold, the two pieces of the mold put together in the direction of the external dimensions of the size of the sum than the size of the drawing of the negative 0.03mm-0.05mm)⊥0.01, ∥0.01, can be grinded to form the part of the molding must be grinded to form;
(6) such as the need for CNC finishing mold nuts, arrange CNC finishing, such as the cavity has a font and mold number need to be engraved processing;
(7) Wire-cut processing: center wire processing insert holes, slant top holes, thimble holes, chirp holes and so on;
(8) Electrical discharge processing: according to the drawings and pulse instruction sheet processing;
(9) Polishing process: in the process card on the roughness of polishing and requirements, in the workpiece with a marker pen to mark the polishing of the region, there are mirror requirements such as the cycle is too late to be rough first to test the mold and then fine polishing;
(10) Assembly;
(11) Test mold.
VII. Main body insert processing technology
(1) Preparation of materials: craftsmen according to the size and shape of the workpiece to define whether a single piece of processing or multiple pieces together, if it is a number of pieces of processing, the craftsmen need to work on the processing of the workpiece row position out of the map;
(2) milling machine processing: the clamp according to the workpiece map or combined with the processor out of the row position map for processing, drilling water holes (water holes plug deepest distance from the transverse water holes 3-4mm), threading holes, drilling, tapping screw holes, drilling, reaming the thimble holes, shaping at the roughing, mold numbering, hanging table to make way for the;
(3) CNC machining: If the workpiece needs CNC roughing, arrange CNC roughing;
(4) Heat treatment processing: indicate the hardness requirements;
(5) Grinding machine processing: grinding six-sided angle ruler, can be grinded to form the part must be ground to form;
(6) such as the need for CNC finishing workpieces, arrange CNC finishing, such as inserts with fonts and mold number need to be engraved processing;
(7) wire-cut processing: center wire processing insert holes, slant top holes, thimble holes and so on;
(8) discharge processing: according to the drawings and pulse instruction sheet processing;
(9) Polishing process: in the process card on the roughness of polishing and requirements, in the workpiece with a marker pen to mark the polishing of the region, there are mirror requirements, such as the cycle is too late to be rough first to test the mold and then fine polishing;
(10) Assembly;
(11) test mold.
VIII. Shaped insert processing technology:
Process 1:
(1) wire cutting processing: the middle wire cut external dimensions cut accurate (A/B view), pull the piece, thickness to leave a margin grinder, molding at the open rough;
(2) Grinding machine processing: grinding thickness, slope, molding;
(3) Electrical discharge processing;
(4) Polishing processing.
Process 2:
(1) Wire-cut processing: medium wire cut profile, insert holes, ejector holes, size cut to size (C view), hanging table and roughing at molding;
(2) Grinding machine processing: grinding height, hanging table, slope, molding;
(3) Electrical discharge machining;
(4) Polishing processing.
IX. Simple insert processing technology
(1) Wire-cut processing: fast wire cut shape margin grinder (A/B view), pull piece, thickness margin grinder;
(2) The shape of the dimensions of the grinding alignment, grinding hanging table, skew, molding;
(3) Electrical discharge machining;
(4) Polishing processing.
X. Round insert processing technology
(1) Centerless grinding: external dimensions grinding alignment;
(2) Grinding machine processing: hanging table at the clear angle;
(3) Wire cutting processing: fast wire cut length (leave 0.1mm grinder allowance on one side), cut thimble holes, exhaust holes;
(4) Grinding machine processing: grinding length, molding.

XI. Slant top processing technology
(1) Wire-cutting processing: center wire cut profile, head to insertion surface to leave a margin grinding with the rest of the dimensions of grinding, pulling piece thickness to leave a margin, I groove roughness to leave a margin grinder;
(2) Grinding machine processing: grinding thickness, I-slot;
(3) Assembly;
(4) Pulse;
(5) Polishing;
(6) milling machine open oil groove.
XII. Slant top seat machining process
(1) Clamping preparation of strips: height size bilateral reserve 1.5 mm, the width of the size of the bilateral reserve 0.5 mm, the length of the bilateral reserve 5 mm to facilitate wire-cutting machining and clamping;
(2) Milling machine processing: drilling and tapping screw holes;
(3) Heat treatment processing;
(4) Grinding machine processing: grinding six-sided angle ruler, the width of the dimensions of the grinding of the right;
(5) wire cutting fast wire processing I-beam groove quasi, pull the piece, the thickness of the thickness to leave a margin grinder, the height of the size of the positive 1.2 mm;
(6) Grinding machine processing: grinding machine external dimensions, with into the thimble plate, the height of the size of positive 1 mm.
XIII. Slant top guide block processing technology
(1) Wire cutting processing: fast wire cutting profile, stay reserved grinder;
(2) Grinding machine processing: grinding six-sided angle ruler, external dimensions grinding accurate;
(3) Milling machine processing: threading holes, screws through the hole;
(4) Wire cutting processing: fast wire cutting slant top guide hole.
XIV. Slider seat processing technology
(1)Preparation of materials;
(2) Grinding machine processing: grinding six-sided angle ruler, external dimensions grinding accurate;
(3) Milling machine processing: drilling threading holes, drilling and tapping screw holes;
(4)Wire-EDM processing: fast wire processing of oblique guide pillar hole;
(5) CNC finishing: milling the size of the molding place.
XV. Pressure block processing technology
(1)Preparation of materials;
(2) Milling machine processing: drilling screws through the hole, molding at the roughing (one side of the reserve 0.3-0.5, grinder);
(3) Grinding machine processing: grinding six-sided angle ruler, external dimensions grinding, molding.
XVI. Locking block processing technology
(1) Prepare materials;
(2) Grinding machine processing: grinding six-sided angle ruler, external dimensions grinding accurate;
(3) Wire-cut processing; fast wire molding;
(4) Milling machine processing: drilling and tapping screw holes.
XVII. Principle of top bar hole processing
The processing of Φ3 or above (including Φ3, Φ4, Φ5 and Φ6) top bar holes adopts milling machine drilling and reaming; Φ3 or below or non-standard top bar holes adopts wire-cutting processing, and the bottom avoids empty space.
XVIII. Principle of threading hole processing
When all kinds of holes need to be processed by wire-cutting, if the circumference of the inner wall is larger than Φ3 (including Φ3), threaded holes must be drilled.
XIX. Trademark processing and the need to throw the mirror surface of the mold
(1) Leave a margin at the logo after CNC milling of the mold kernel;
(2) Wire cutting center wire processing: trademark insert holes;
(3) Electrical discharge machining: hanging table depth quasi;
(4)Match the trademark core and install the fixture;
(5)Remaining allowance at the trademark pulse picking up flat;
(6) Polishing.
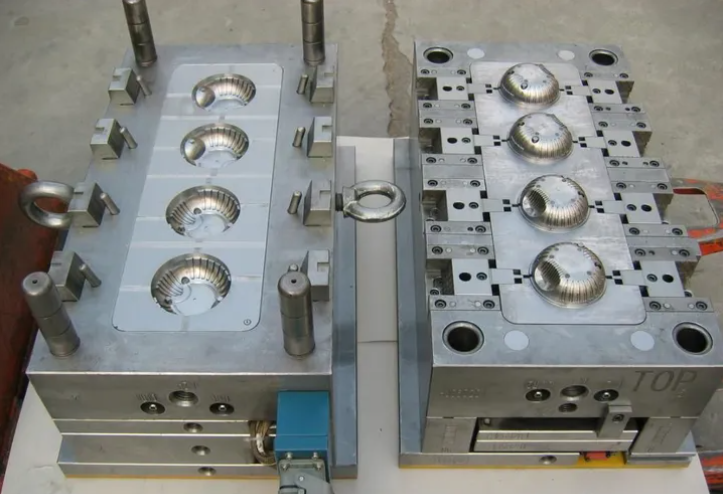
XX. Mold frame processing technology
(1) Milling machine processing: chamfering the inner frame, drilling screw holes, thimble holes, water holes, sprue cup holes, slant top holes;
(2) CNC machining: milling sprue cup countersinking holes, slant top seat holes, guide block holes, line slot, hot runner mold A plate needs CNC machining, mold foot engraving processing.
XXI. Post-molding process of mounting bracket with grid-like reinforcement bars
This kind of mounting bracket after the mold rib processing according to different categories of molds, choose a different processing technology.
(1) One type of mold we directly use the whole electrode to ensure the unity of the product;
(2) When choosing the machining process for non-class one mold, it can be deployed according to the actual machining quantity. Electrode can be done as split or whole, if the rib position is through slot, it can be rough by wire cutting first, and then finish by grinder.
XXII. Workpieces requiring wire-cutting jigs or electrodes, batch pulsing
For some workpieces (e.g., the core of multifunctional two-plug jack) that need wire-cutting jig or electrode, the machining process of workpieces with batch pulse is as follows:
(1) CNC draws the layout;
(2) Wire cutting takes the drawing and processes the fixture or electrode according to the dimensions;
(3) wire cutting processing is completed, such as electrode still need CNC processing will be handed over to the CNC electrode, the fixture will be forwarded to the clamp;
(4) CNC machining electrode, and discharge diagram;
(5) Pulse processing;
(6) Polishing.
XXIII. Calculation of support column height
The height of the support column of the mold frame is 0.08-0.1mm higher than the foot of the mold below 3030, 0.1mm higher at 3030, 0.1-0.12mm higher at 3535, and 0.12-0.15mm higher at 3535 and above.
XXIV. Ejector pin processing technology
Φ2 and above thimble cutting machine cutting length to leave a margin grinder, grinder processing length dimensions ground to the right (clampman own processing);
Φ2 below the thimble wire cutting processing size cut accurate. Flat thimbles and barrels are processed by wire-cutting machine, grinding machine, and grinding to the correct length and size.
If you have rapid prototype / mould customization needs,please contact us!
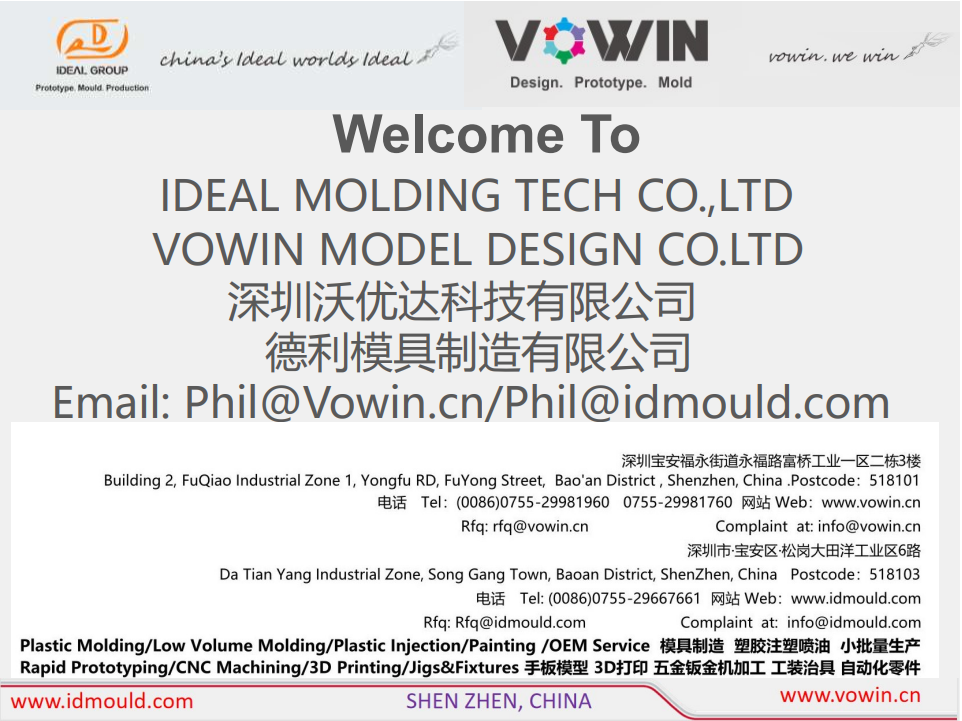
Posts by Topic
Recent Posts
- What is the process of mold manufacturing?
- What should be paid attention to the polishing of injection molds?
- What is easy to ignore when maintaining and overhauling injection molds?
- What are the 6 systems of plastic molds?
- What are the methods of strengthening the surface of injection molds?
- What are the methods of insulation for injection molds?
- How to solve the problem of injection mold release difficulty?
- How can we increase the brightness of ABS injection molded parts?
- What are the common problems of mold maintenance and how to solve them?(1)
- What are the common problems of mold maintenance and how to solve them?(2)