Resources
What are the common problems of mold maintenance and how to solve them?(1)
Release time:2024-03-27
What are the common problems of mold maintenance and how to solve them?(1)
Often experience customers say you have problems with the mold, and are said to be your mold quality problems, but never reflected on the use of the process there is no problem, the following Kexiang mold manufacturer editor-in-chief to share some of the common problems in the maintenance of the mold and the solution.
1. Before using the punch, you should pay attention to
①Clean the punch with a clean rag.
② Check the surface for scratches and dents. If there are, remove them with oil stone.
③ Oil the punch in time to prevent rust.
④ Be careful not to have any tilt when installing the punch, use soft material tools like nylon hammer to knock it gently, and tighten the bolt only after the punch is correctly positioned.
2. Installation and debugging of punching die
Installation and adjustment of the die must be especially careful. Because the die, especially the large and medium-sized die, is not only expensive, but also heavy and difficult to move in minute quantities, the safety of human beings should always be put in the first place. Infinite device die in the upper and lower die should be added between a cushion board, in the punch press table clean up, will be the state of the mold to be tested mold placed in a suitable position on the table.
According to the process documents and die design requirements selected by the press slider stroke, in the mold before moving on the table to the lower dead center and greater than the mold closing height of 10 ~ 15mm position, adjust the slider linkage, move the mold to ensure that the die handle aligned with the die handle holes and to achieve the appropriate height of the clamping die. In general, the blanking die should be fixed with the lower die first (not tightened) and then the upper die (tightened), and the T-bolts of the pressure plate should be tightened with the appropriate torque wrench (lower die) to ensure that the same bolts have the same and ideal pre-loaded clamping force. It can effectively prevent the manual tightening of threads due to physical strength, gender, feel the error caused by the pre-tightening force is too large or too small, the same thread pre-tightening force is not the same, which can cause the upper and lower molds in the process of stamping the wrong shift, gap changes, nibbling stripping edge and other failures.
Before the die test, fully lubricate the die and prepare the material for normal production, and start the die in the empty stroke for 3~5 times to confirm the normal operation of the die before the test punch. Adjust and control the depth of the convex die into the concave die, check and verify the performance and operational flexibility of the die guiding, feeding, pushing and unloading, side pressure and elastic pressure and other institutions and devices, and then make appropriate adjustments to make it reach the best technical state. The large, medium and small-sized punching dies are test-punched 3 pieces, 5 pieces, 10 pieces for the initial inspection of production stoppage, and then test-punched 10 pieces, 15 pieces, 30 pieces for re-inspection after passing the test-punched, after scribing and testing, punching surface and burr inspection, all the dimensions and the shape and positional accuracy are in line with the requirements of the drawings before delivery to the production.
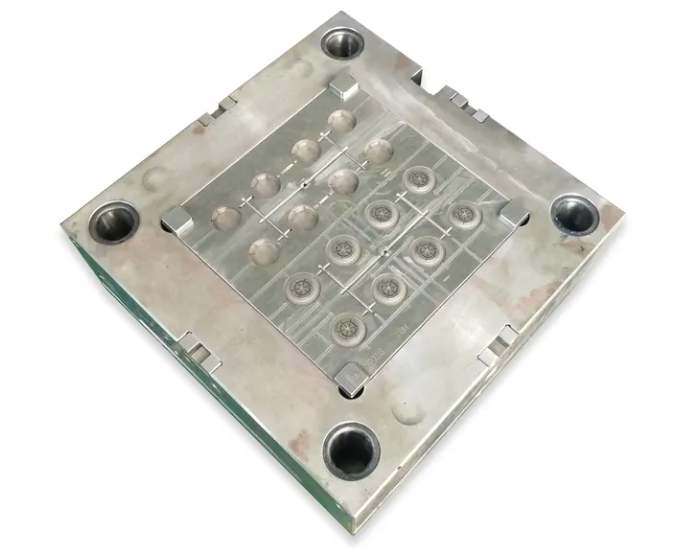
3. Stamping burrs
① Mold clearance is too large or uneven, should re-adjust the mold clearance.
② Mold material and heat treatment is not appropriate, resulting in a concave die inverted cone or edge is not sharp, should be reasonable selection of materials, mold working part of the material with carbide, heat treatment needs to be reasonable.
③ Stamping wear, should grind the punch or insert.
④ Convex mold into the concave mold is too deep, should be adjusted into the depth.
⑤ The guiding structure is not precise or improperly operated, the guide pillar and guide sleeve in the mold should be overhauled and the guiding precision of the press should be regulated.
4. Waste jumping
It may be caused by larger clearance of the mold, shorter convex die, influence of material (hardness, brittleness), too high speed of stamping, adhesion caused by too sticky stamping oil or too fast oil droplet, vibration of stamping and dispersion of chips, vacuum adsorption and insufficient demagnetization of the core of the die, etc. All of these may cause the waste to be brought to the surface of the die.
① Check the sharpness of the cutting edge. The sharper the edge is, the easier it is to cause the scrap to bounce back, and for thin stainless steel materials, you can use a beveled edge.
② For more regular waste, you can increase the complexity of the waste or add polyurethane top bar on the punch to prevent jumping waste, and increase the scratches on the edge side of the concave mold.
③ Whether the clearance of the mold is reasonable. Unreasonable mold clearance, easy to cause the waste rebound, for small diameter hole clearance reduced by 10%, the diameter is greater than 50 mm, the clearance should be enlarged accordingly.
④ Increase the depth of the mold. Each station mold stamping, the requirements of the mold is a certain amount of entry, the amount of entry is small, easy to cause the scrap rebound.
⑤ Pay attention to whether there is oil on the surface of the processed material.
⑥ Adjust the stamping speed and pay attention to the concentration of stamping oil.
⑦ Adopt vacuum adsorption.
⑧ Demagnetize the punches, inserts and materials.
5. Pressure, scratch
① The material belt or mold has oil, waste chips, resulting in pressure injuries, need to wipe the oil and install automatic air gun to remove waste chips.
② Mold surface is not smooth, should improve the mold surface finish.
③ The surface hardness of the parts is not enough, the surface needs to be chromium-plated, carburized, boron infiltration and other treatments.
④ Material strain and destabilization, reduce lubrication, increase compressive stress, adjust the spring force.
⑤ Maintain the mold of jumping waste material.
⑥ The product scrapes to the mold positioning or other places during the operation to cause scratches, need to modify or reduce the positioning of the mold, and caution the operators to hold lightly during the operation.
6. Scratch on the outer surface of the workpiece after bending
① Raw material surface is not smooth, need to clean, calibrate the original material.
② Molding into the block has waste, need to remove the waste chips into the block between.
③ Molding block is not smooth, the molding block plating, polishing, convex and concave die to improve the finish.
④ Cnvex mold bending radius R angle is too small, increase the convex mold bending radius.
⑤ Mold bending clearance is too small, adjust the upper and lower mold bending clearance.
⑥ Concave die forming block with roller molding.
7. Leakage of punched holes
Leakage of punched holes, generally by the punch is broken but not found, after repairing the mold leakage of punches, punches sinking and other factors caused by the repair of the mold should be the first piece of confirmation, compared with the sample, check whether there is a missing phenomenon, the punch sinking, should improve the hardness of the upper die pad.
8. Abnormal stripping
① Stripper plate and convex mold with too tight, stripper plate tilt, isometric screw height is not uniform or other stripper device is not appropriate, should be repaired stripper, stripper screws using a combination of casing and socket head cap screws.
② Mold clearance is small, the punch in the detachment of the material requires a lot of demolding force, resulting in the punch is bitten by the material, need to increase the lower die clearance.
③ The concave mold has inverted cone, trimming the concave mold.
④ The drop hole of concave mold and the leakage hole of lower mold seat are not correct, fix the leakage hole.
⑤ Check the condition of processed material. (5) Check the condition of the material to be processed. The material is dirty and adheres to the die so that the punch is bitten by the material and cannot be processed. The warped and deformed material will clamp the punch after punching. When the warped and deformed material is found, it needs to be smoothed out and then processed.
⑥ The edge of the punch and the lower die should be sharpened in time. Sharp edge of the mold can process a beautiful cut-off surface, blunt edge, it requires additional punching pressure, and the workpiece section is rough, resulting in a great resistance, resulting in punches by the material bite.
⑦ Appropriate use of beveled edge punches.
⑧ Minimize wear and tear, improve lubrication conditions, lubricate the plate and punch.
⑨ Spring or rubber elasticity is not enough or fatigue loss, timely replacement of the spring.
⑩ Guide column and guide sleeve clearance is too large, rework or replace the guide column guide sleeve.
◎Parallelism error accumulation, regrinding assembly.
◎The hole on the push piece block is not perpendicular, so that the small convex mold deviation, repair or replace the push piece block.
◎Convex mold or guide column installation is not perpendicular, reassembly to ensure perpendicularity.
Ideal Vowin Group is an injection mould & CNC machining factory, support rapid prototyping, 3D printing, mould customization, we have recently helped our customers to complete many big projects, for more details, please visit our official website: www.idmould.com / www.vowin.cn.
If you have relevant needs,please contact us!
If you have relevant needs,please contact us!
WhatsApp: +8617369230494
Wechat: 17369230494
E-mail: yuki@idmould.com/yuki@vowin.cn
Posts by Topic
Recent Posts
- What do we need to pay attention to the plastic mold machining process and machining procedures?
- What kinds of plastic mold materials?
- What is the process of mold manufacturing?
- What should be paid attention to the polishing of injection molds?
- What is easy to ignore when maintaining and overhauling injection molds?
- What are the 6 systems of plastic molds?
- What are the methods of strengthening the surface of injection molds?
- What are the methods of insulation for injection molds?
- How to solve the problem of injection mold release difficulty?
- How can we increase the brightness of ABS injection molded parts?